SERVICES
Rubber Compression
Another assistance we can offer is our specialized rubber compression molding services. This method is perfect for applications that still call for traditional processes as the most efficient and reliable choice. You can utilize diverse grades of silicone, thermoset rubber, and components with heavy cross-sections to create durable, high-quality rubber parts.
Our rubber department is equipped with presses featuring 30” x 30” platens and a 24” ram, which allows us to handle large, intricate molds with precision. Whether you need compression or transfer molding, we can make it happen. We can also help you decide on the best approach for your specific needs.
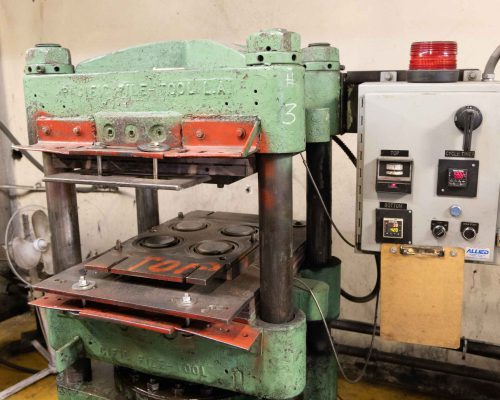
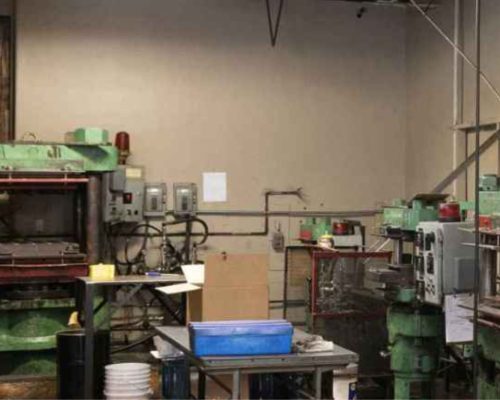
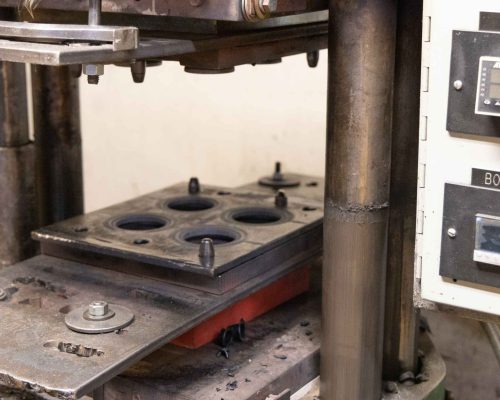
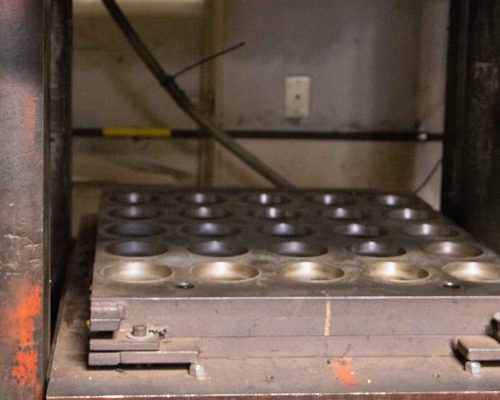
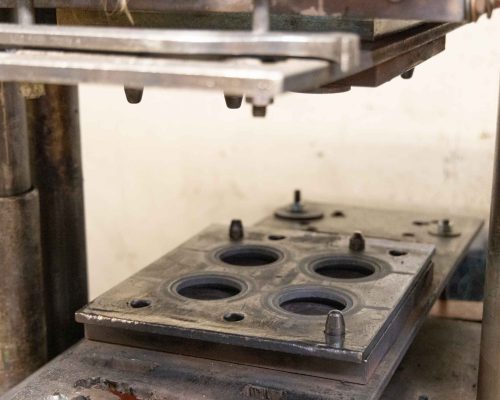
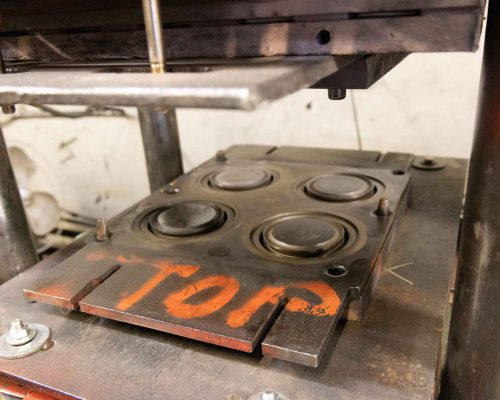
Why Choose Rubber Compression Molding?
Your best option is rubber compression when you need to produce parts that strictly require consistency in material distribution. Great examples are items with complex shapes or heavy sections.
You must determine what rubber molding application a particular project needs. Sometimes, a product needs high temperature and high-pressure conditions to maintain its consistent integrity and performance regardless of environmental elements. Excess material is managed during the compression molding by filling the mold’s overflow grooves after uncured rubber is placed in the mold. This ensures proper demolding and prevents issues such as flashing.
The Compression Molding Process
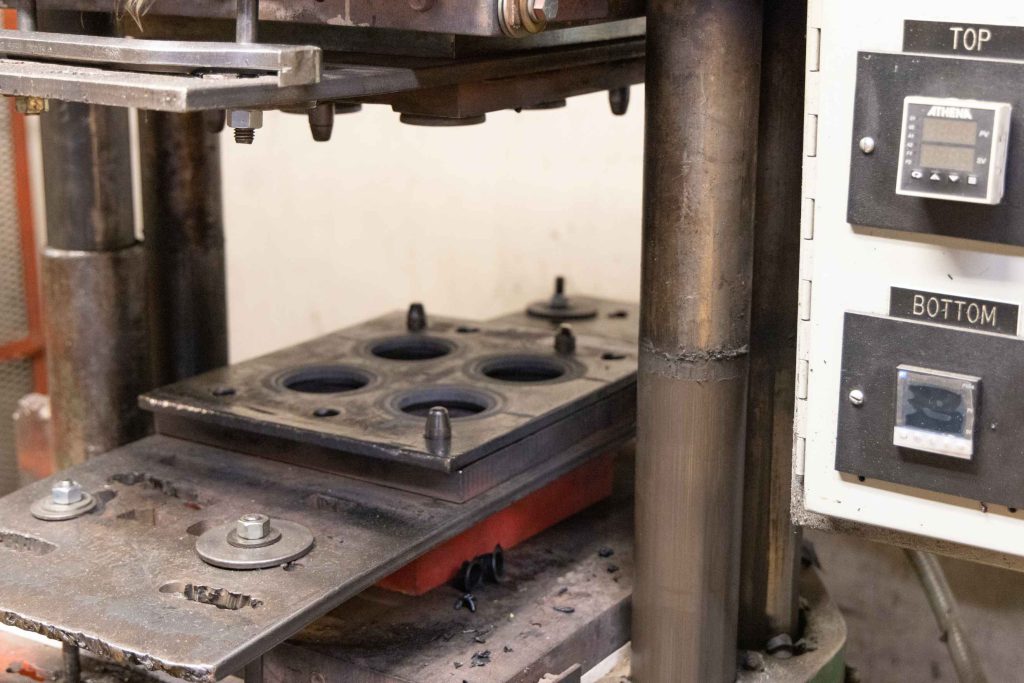
The compression molding process typically involves the following steps:
- Pre-form Preparation: The uncured rubber is prepared into a pre-form, a chunk of rubber roughly the shape of the final product.
- Mold Preparation: The mold is prepared by applying a release agent to the mold cavity to prevent the rubber from sticking.
- Pre-form Placement: The pre-form is placed into the mold cavity.
- Compression: The mold is closed, and pressure is applied to the pre-form to force it into the mold cavity.
- Curing: The rubber is cured under heat and pressure, causing it to take the shape of the mold cavity.
- Demolding: The mold is opened, and the cured rubber product is removed.
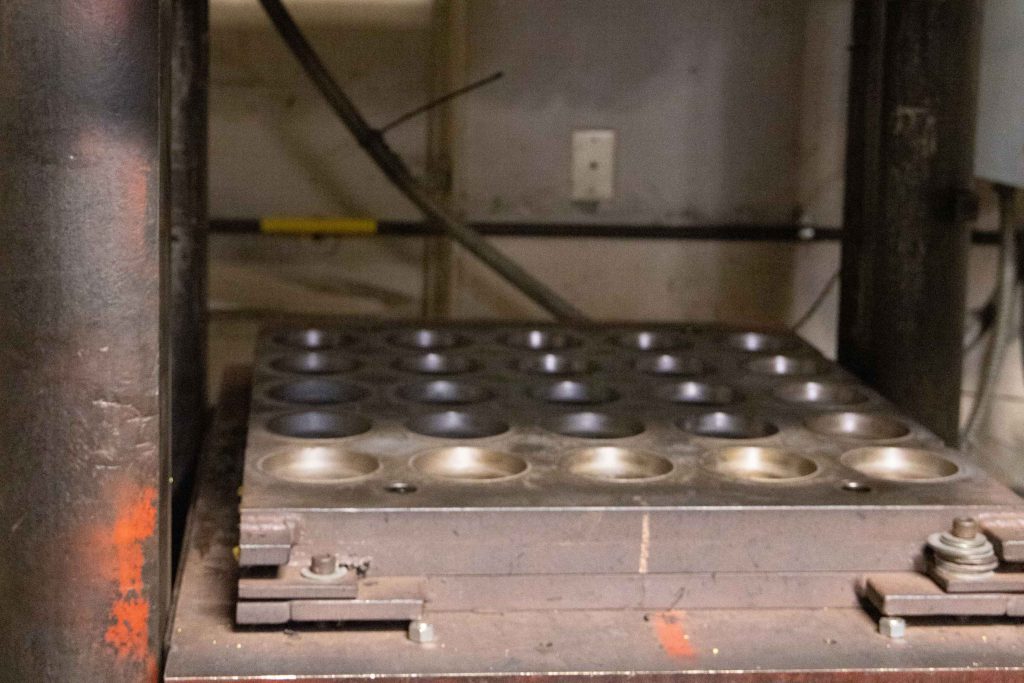
Compression Molding Tolerances
Compression molding tolerances refer to the allowable variations in the dimensions of a molded rubber product. These tolerances ensure the final product meets the required specifications and performs as expected. Several factors can affect compression molding tolerances:
- Shrinkage: Rubber materials can shrink during curing, affecting the final product’s dimensions.
- Mold Design: The design of the mold can influence the tolerances of the final product. For instance, a mold with a complex shape may require tighter tolerances than a simpler mold.
- Curing Process: The curing process can also impact the tolerances. A longer curing time may result in a more accurate product.
Understanding and controlling these factors is essential for producing high-quality rubber parts with precise dimensions.
Compression Mold Preparation
- Set the mold by cleaning it first
- Apply the release agent.
- Heat the charge to increase the viscosity in preparation for the loading
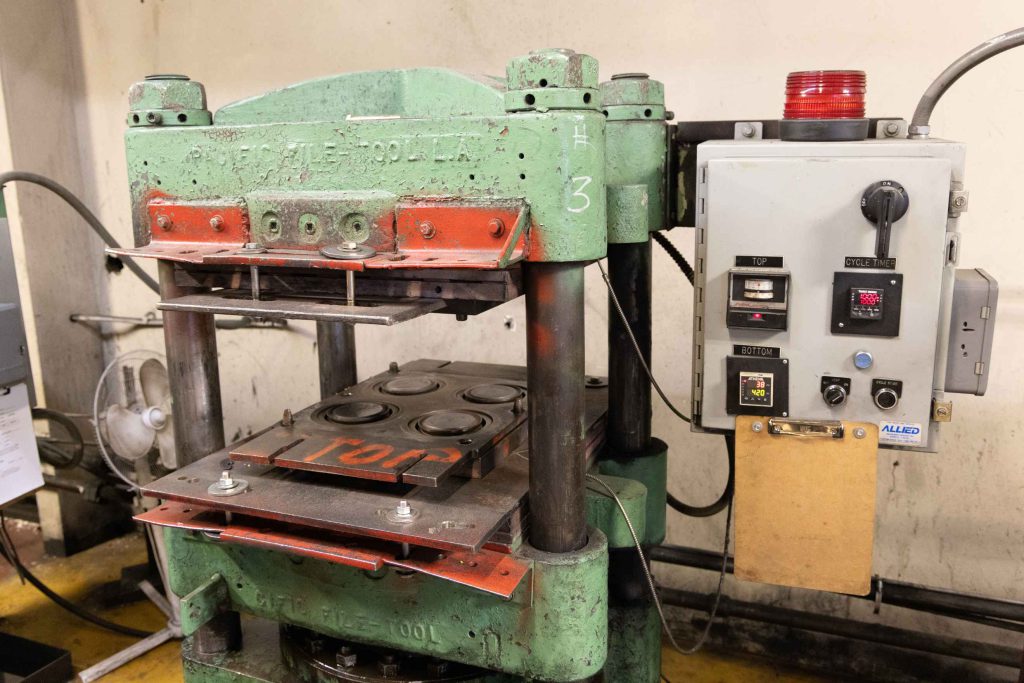
Charge Preparation
Charge preparation is the most laborious phase in compression molding because, unlike the other processes, it is not mostly automated.
You can apply the compression molding method to various compression-set materials, simple or complex compressed mold designs, and varied cavity sizes, formattings, and conditions. Preparation prepares the material for compression, including Unpacking, cleaning, cutting, sizing, weighing, and heating.
This process is suitable for simple shapes and low to medium production volumes. It involves placing a pre-heated mass into a mold and then closing the upper mold to shape the material. Compression molding is a time-tested method that can handle many rubbers. It’s also low maintenance and inexpensive to tool, with production costs falling as volume increases.
During the compression molding process, excess material is managed by filling the mold’s overflow grooves after uncured rubber is placed in the mold. This ensures proper demolding and prevents issues such as flashing.
Services
Materials and Applications for Molded Rubber Products

Natural Rubber
A natural, biodegradable rubber material often used for applications requiring high elasticity and flexibility

Synthetic Rubber
Man-made rubber material for high durability and chemical resistance applications.

Silicone Rubber
A synthetic rubber material known for its high-temperature resistance and flexibility, ideal for various industrial applications.

Neoprene
A synthetic rubber material with high resistance to oil and chemicals, commonly used in demanding environments.
These materials are used in a wide range of applications, including:
- Industrial Applications: Such as gaskets, seals, and vibration mounts.
- Automotive Applications: Including engine mounts, suspension components, and seals.
- Medical Applications: Including seals, gaskets, and implantable devices.
Each material offers specific benefits, making them suitable for different molded rubber products and applications.
Compression molding
These materials are used in a wide range of applications, including:
- Industrial Applications: Such as gaskets, seals, and vibration mounts.
- Automotive Applications: Including engine mounts, suspension components, and seals.
- Aerospace Applications: For seals, gaskets, and vibration mounts.
- Medical Applications: Including seals, gaskets, and implantable devices.
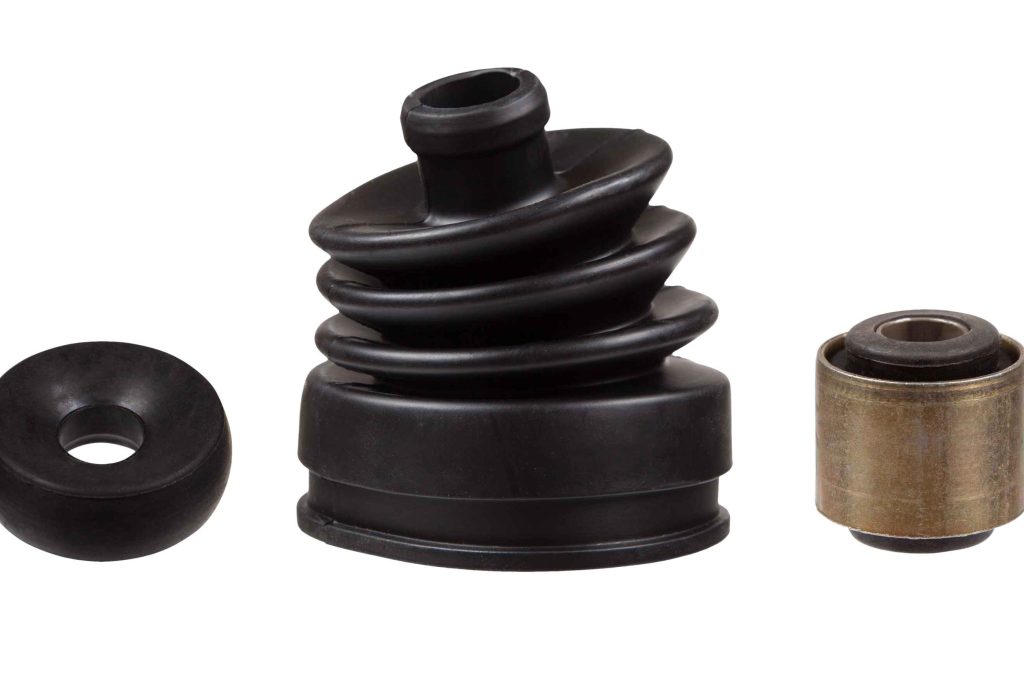
Custom Solutions and Quality Assurance in Molded Rubber Products
We continuously improve our processes to deliver custom rubber components that meet strict performance and durability standards. We are particular with the details, ensuring they meet your specifications and serve the products’ purpose. Our team handles quality checking at every step of the molding process to provide the highest quality.
Additional Benefits of Partnering with Us
- We have the equipment that can accommodate your rubber injection molding specifications.
- We prioritize you to ensure on-time product delivery.
- We propose cost-effective solutions so we can both have a win-win solution.
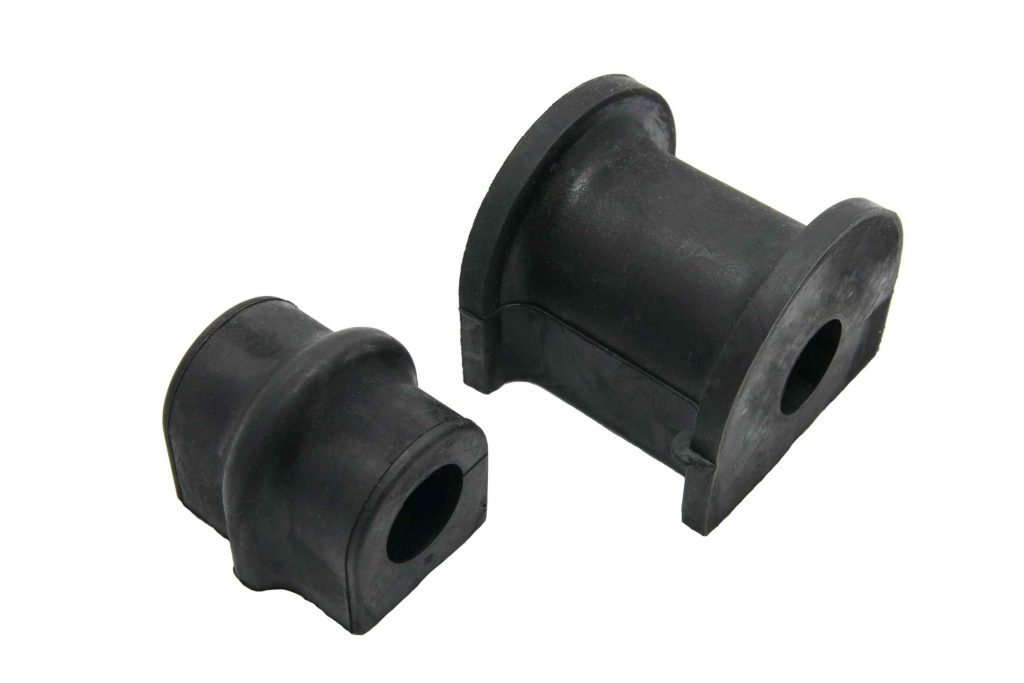
Be Our Partner
Be our partner in the rubber compression molding solutions you want for your business. Our over fifty years of experience have helped us learn what works and what does not. Contact us to learn more about what we can do or get a quote for your next project.
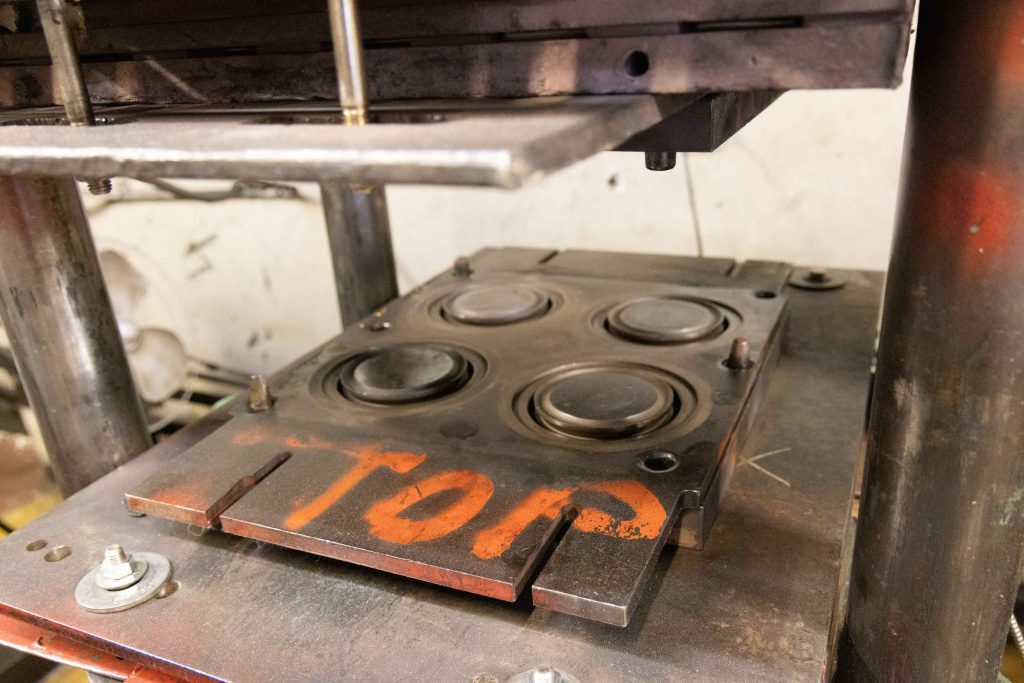
Resources
New to injection molding and unsure where to start? Our comprehensive guide has all the answers to help you choose the best plastic injection molding service provider.
There is no better way to show our capabilities to you than sharing our experiences working with our partners.
We have prepared these articles to help you as you venture further into plastic injection molding and understand the plastics industry better.