Our Services
Custom Plastic
Injection Molding
- Reliable quality and consistency
- Design-to-production support
– Precision manufacturing
– Low to high production runs - Tailored to unique client needs
- Sustainable materials and processes
- Fast, reliable project completion
Our Services
Rubber Compression
- Precision molding of complex, varying sizes, and intricate designs
- Presses with 30” x 30” platens and a 24” ram
- High-volume, high quality
Our Products
Tree Felling Wedges
- Highest energy transfer
- Durable, high-impact plastic, less worry about chipping or breaking
- Lightweight, tough, high visibility
- Saw-safe features protect chainsaws, ensuring safety even in close quarters
- Customizable colors for personal branding
- Bright, visible colors improves safety and wedge identification in rugged terrain
Our Products
Lambing Supplies
- Safe, stress-free handling of lambs and ewes
- Transport multiple lambs simultaneously and effortlessly
- Easy sterilization, with durrable materials to withstand difficult farm conditions
- OB Leg Snare and Pull-EZE ensure security for smooth, safe deliveries
- Farmer-centered, practical, and designed to meet the demands of livestock care
Industries
We Serve
Beaver State Plastics proudly provides custom injection molding and rubber compression services for various industries, including agricultural, industrial, construction, manufacturing, food services, consumer products, and many others associated with our parent company, Quadel Industries.
Beaver State Plastics is your reliable, on-time custom plastic injection molding partner. We are a dependable partner every step of the way.
Known for producing precision and high-quality products, our team fosters a close customer relationship noted by reliability and high levels of communication. Whether you’re a small business or a large corporation, Beaver State Plastics is committed to providing you with the best products and services to meet your needs. Explore our site to discover how we can support your company with high-quality, reliable solutions.
engineering
- Automotive: Interior and exterior components like dashboards, consoles, and body panels
- Electronics: Enclosures, connectors, and insulation for electronic devices
MANUFACTURING
- Industrial Machinery: Plastic gear housings, pulleys
- Tooling and Molding: Injection molds and tooling components
- Packaging: Containers
CONSUMER PRODUCTS
- Toys: Action figures, building blocks, and playsets
- Housewares: Kitchenware, storage containers, and furniture
- Electronics: Cell phone cases, computer peripherals, and gaming accessories
FARMING AND AGRICULTURE
- Irrigation: Pipes, fittings, and drip irrigation systems
- Greenhouse: Structural components, covering materials, and plant pots
- Animal Husbandry: Feeding troughs, waterers, and fencing materials
FORESTRY
- Equipment: Protective gear, helmets, and safety eyewear
- Signage: Warning signs, trail markers, and informational plaques
- Infrastructure: Bridge components, retaining walls, and erosion control barriers
FOOD SERVICES
- Food Packaging: Disposable food containers, trays, and lids
- Kitchenware: Cutting boards, utensils, and storage containers
- Tableware: Plates, cups, and cutlery
Our Customers
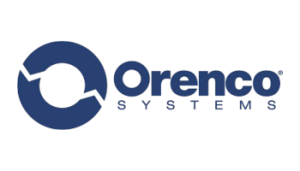
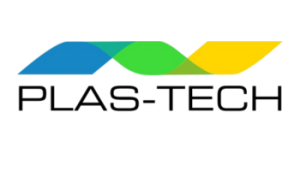
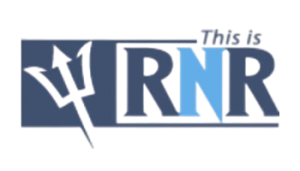
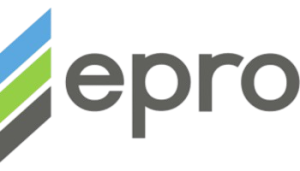
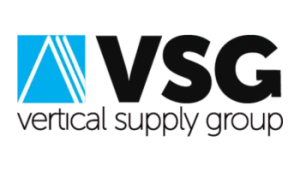
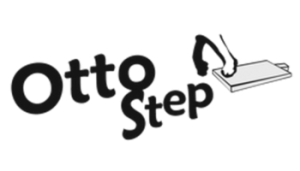
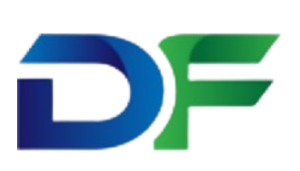
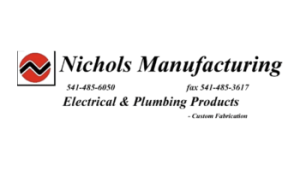
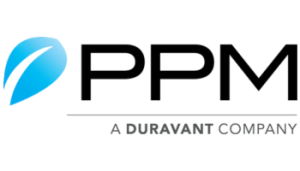
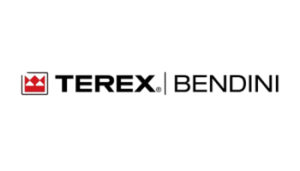
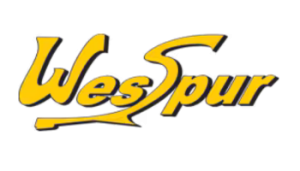
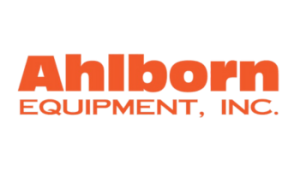
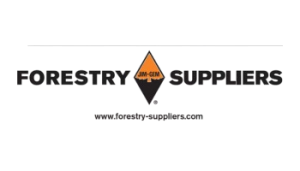
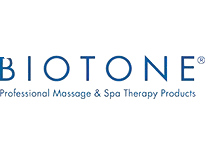
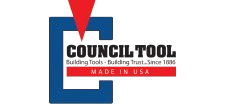
Your Trusted Partner for Reliable and Repeatable Injection Molding
Have a Question?
Top Frequently Asked Questions: Plastic Injection Molding
We understand that there can be more questions about plastic injection molding than we have presented here. Please send your questions by filling out this form. We are always willing to help and answer your questions about injection molding.
Plastic injection molding is a precise manufacturing method where raw plastic is melted and injected into molds under high pressure, creating specific parts efficiently and consistently.
This process is essential in producing a wide range of plastic components.
Each component of an injection molding machine—the mold, the clamping unit, and the injection unit—is pivotal for maintaining precision and efficiency throughout production.
Mold temperature is important in injection molding because it helps ensure the flow of the melted material once it is injected into the machine. Mold temperature directly influences the durability and precision of the final output, which is the final moulded part.
Yes, mold temperature plays a major role in your final molded product. Maintaining the correct mold temperature ensures improved quality and performance of the molded product. Typically, mold temperatures range from 50°C to 120°C (122°F to 248°F), depending on the type of plastic material being used. For instance, engineering plastics like polycarbonate may require higher mold temperatures to ensure proper flow and surface finish, while materials like polypropylene might need lower temperatures. Monitoring and controlling these temperatures precisely is crucial as it directly affects the cooling rate and, consequently, the cycle time, dimensional stability, and surface quality of the molded parts.
Selecting the appropriate materials for plastic injection molding is vital to ensuring the quality of the finished item. Many thermoplastics exist, each with distinct attributes and possible uses. Recognizing these material characteristics is essential for manufacturers to identify the most suitable choice tailored to their particular requirements.
The range of plastic resins available, including widespread options such as ABS and polycarbonate and specialized formulations aimed at specific applications, is crucial in determining success during the plastic injection molding. These plastics must be meticulously selected considering their performance attributes, expense implications, and compatibility with the intended use they’re being molded for.
Initial tooling costs in injection molding are primarily influenced by the part’s size and complexity, the number of cavities in the mold, and the materials selected for mold construction.
Understanding these factors can help budget the project effectively. For example, tooling costs can range from $5,000 to $100,000 or more, depending on these factors. A simple mold for a small, uncomplicated part might cost between $5,000 and $10,000. In contrast, a complex mold with multiple cavities and intricate features can exceed $50,000. Additionally, the choice of mold material, such as hardened steel for durability, can increase costs significantly compared to aluminum molds, which are typically less expensive but may wear out faster. Consulting with the injection molding company will give you the initial quote you need.
Both compression molding and injection molding is intended to produce plastic parts that industries can use. The main difference is how the plastic material is introduced into the mold.
In compression molding, a pre-measured quantity of material is poured into a heated mold cavity, and then the mold is closed and compressed. Large, robust rubbers and silicone-made items are frequently produced with compression molding. In injection molding, a screw-driven heating system melts plastic into a closed mold cavity under tremendous pressure. This process is mainly used to mass-produce complex plastic parts.
Manufacturers can reduce excess material and waste in injection molding by adopting efficient design strategies, optimizing material usage, and choosing appropriate mold base materials.
This approach leads to more sustainable manufacturing practices and cost savings. For instance, the injection molding process boasts a high production efficiency, often achieving cycle times as short as 15 to 120 seconds per part, depending on the complexity and size of the product. This rapid cycle time allows for the production of thousands of parts in a single day, significantly reducing manufacturing costs.
Furthermore, injection molding’s precision is demonstrated by its ability to maintain tight tolerances, often within 0.01 mm, ensuring consistent quality across large production runs. Additionally, injection molds’ durability is noteworthy, with some molds capable of producing over a million parts before requiring significant maintenance or replacement. These metrics underscore the reliability and cost-effectiveness of plastic injection molding as a manufacturing process.
Testimonials
What Our Clients Say
"We have been very pleased with the service we have received from your company."
Construction Products
"Rashell's customer service is great!"
Electrical & Plumbing Products
Resources
New to injection molding and unsure where to start? Our comprehensive guide has all the answers to help you choose the best plastic injection molding service provider.
There is no better way to show our capabilities to you than sharing our experiences working with our partners.
We have prepared these articles to help you as you venture further into plastic injection molding and understand the plastics industry better.